T: 01202 779455M: 07808 666380E: Contact us
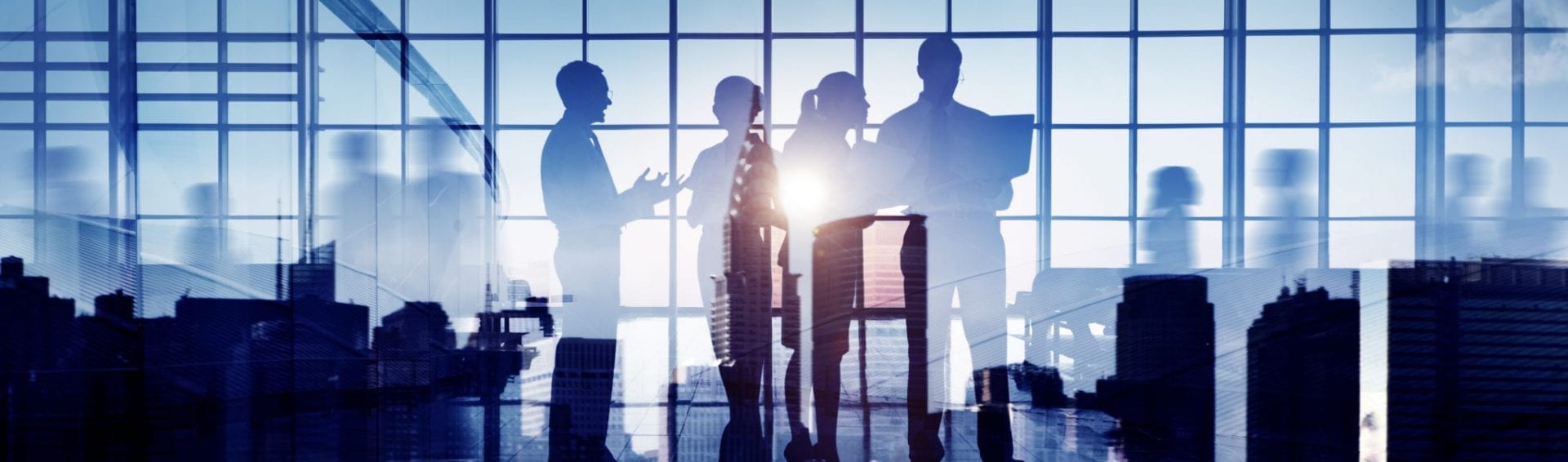
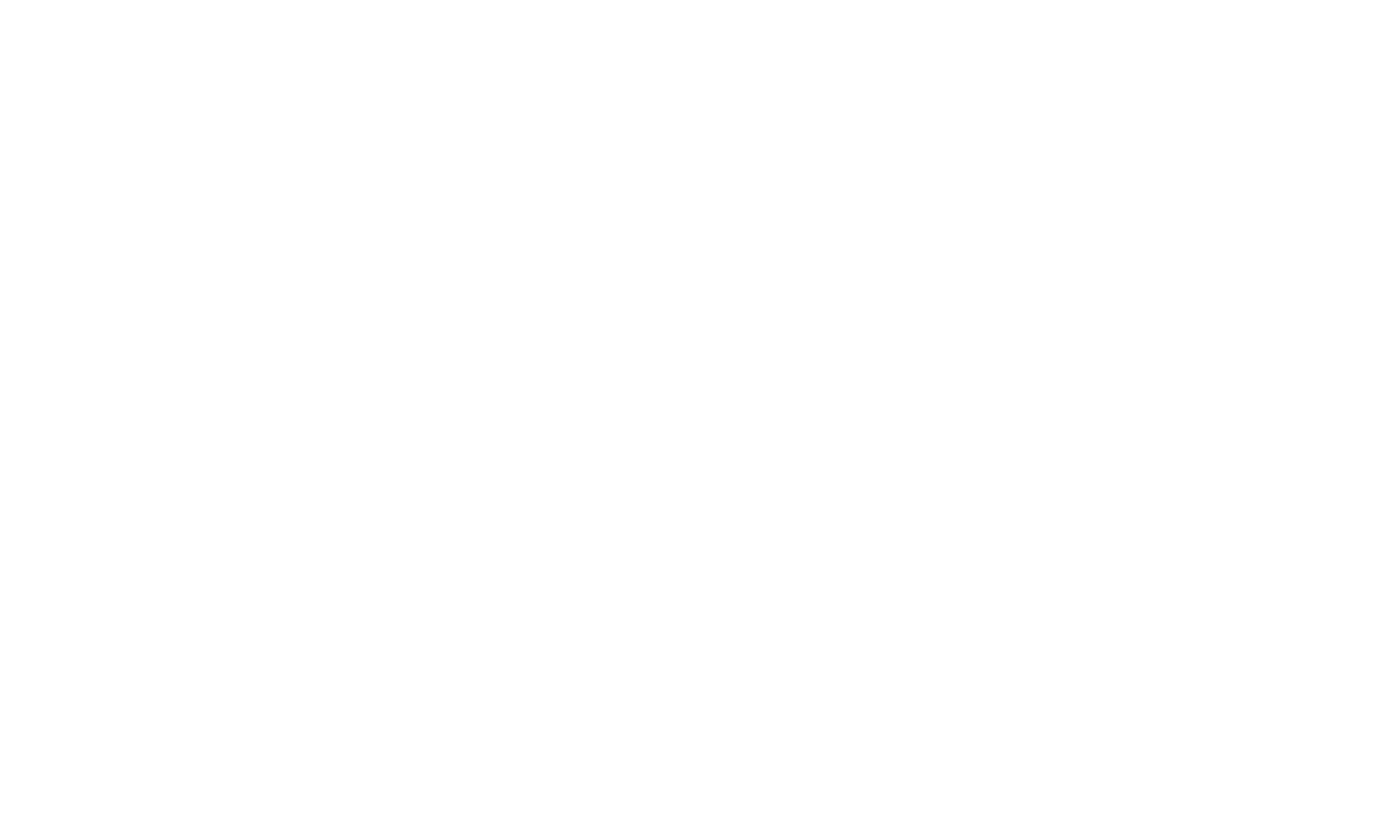
Business Process Improvement
Business Process Improvement
Business process improvement (BPI) is a strategic planning methodology aimed at identifying the operations or employee skills that could be improved to encourage smoother procedures, more efficient workflow and overall business growth. This process can also be referred to as functional process improvement.
The purpose of business process improvement is to meet customer demands and business goals more effectively. Rather than drawing out change management in incremental steps, BPI seeks to bring drastic transformation in an organisation’s performance. In IT, business process improvement addresses the root causes of process or system deficiencies to harmonise IT and business goals. Process mapping, which assesses business operations to pinpoint problem areas and adjust workflow, is often the first step in a larger business process improvement effort.
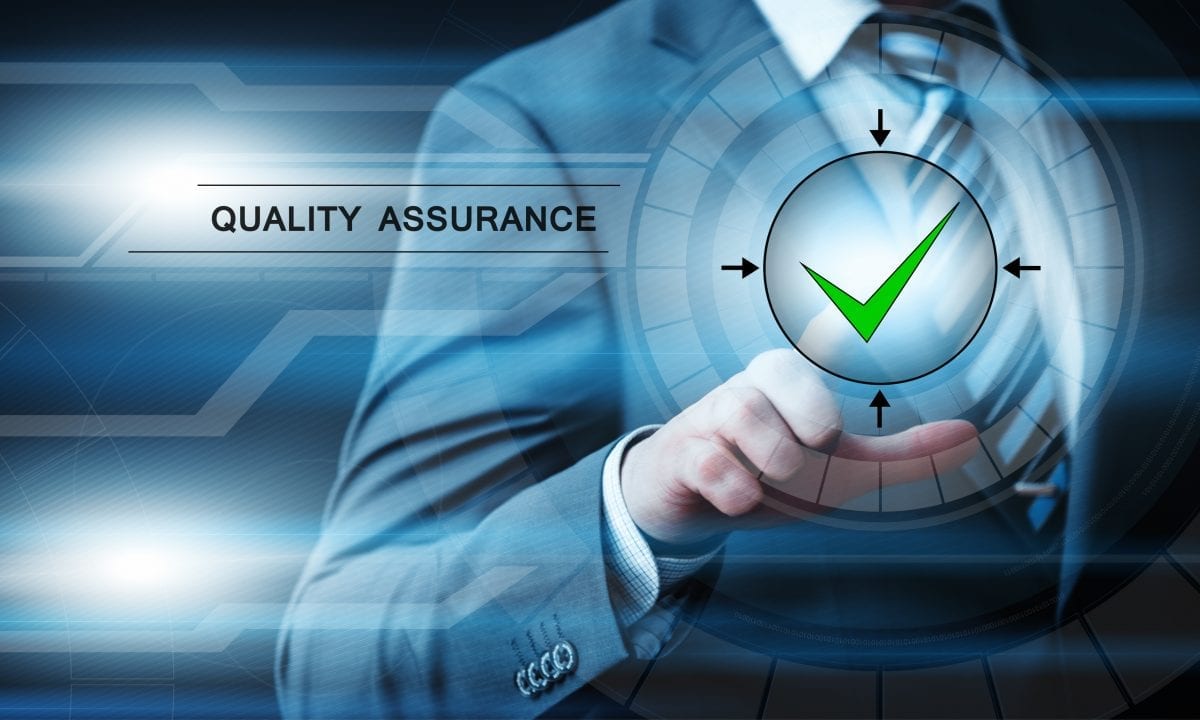
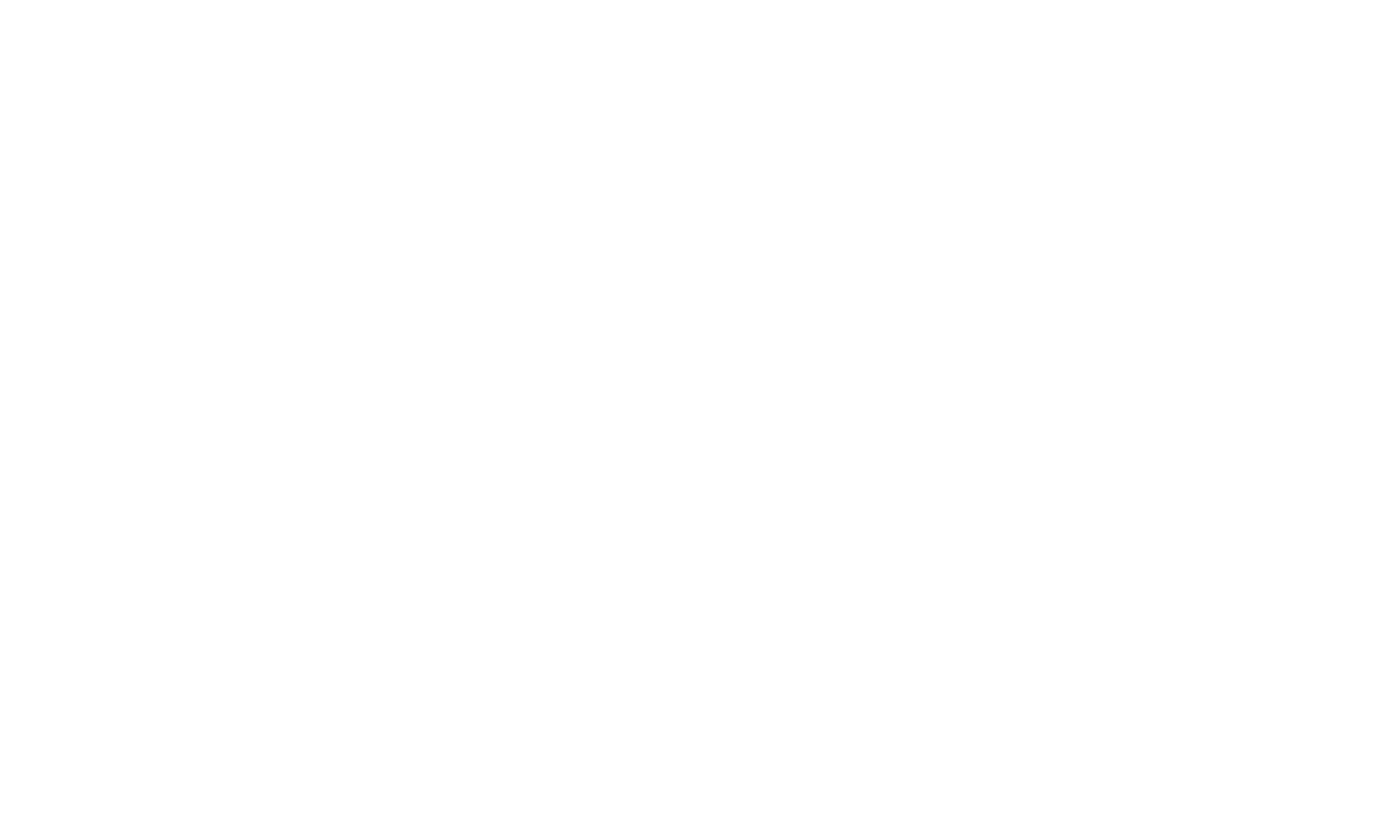
The Main Standards We Work With
We work with all Standards across all industries and sizes of organisations, so we tailor our services to suit your business requirements and resourcing needs.
- ISO 9001:2015 – Quality Management Systems
- ISO 14001:2015 – Environmental Management Systems
- ISO 45001:2018 – Occupational Health and Safety Management Systems
- ISO 27001:2013 – Information Security Management Systems
- BS EN 1090- CE Marking for Structural Steel and Aluminium Fabricators
We can also offer help and advise on other standards, please get in touch to discuss your requirements.
The Process Approach, which is referred to throughout the ISO Management Standards, is intended to continually enhance business efficiency, and effectiveness in achieving the business objectives and targets.
Plan-Do-Check-Act (PDCA) methodology is a tool used to continually define, implement and control improvements throughout each business process, truly integrating continual improvement throughout all that you do.
Our Experts can assist and guide you with continually improving your business processes, whether it be as part of a project to upgrade your business systems for ISO Certification readiness, or simply to improve what you already do well.
We have developed strategies and tools to facilitate this process effectively and efficiently for your business, saving you hours that you just don’t have, and getting you back to what you do best.
Before beginning any sort of BPI initiative, companies must be sure that they understand the three core objectives behind BPI:
- Effectiveness — Does the process meet customer needs?
- Efficiency — Does it cut down on the usage of resources?
- Adaptability — Is the process flexible enough to change as requirements change?
Once a company understands the motivation behind BPI, they can move on to the 10 Steps:
- Develop the Process Inventory: Identifying and Prioritizing the Process List — As with most projects, this step involves figuring out where to start.
- Establish the Foundation: Avoiding Scope Creep — After figuring out what the improvement effort will be focused on, Step 2 involves the scope definition document, which is the blueprint for the rest of the process.
- Draw the Process Map: Flowcharting and Documenting — This step involves mapping the business process so everyone involved understands how the process works and where handoffs occur between departments.
- Estimate Time and Cost: Introducing the Process and Cycle Time — Step 4 helps the company summarise the labour required to deliver a business process and how long the process takes.
- Verify the Process Map: Gaining Buy-in — In Step 5, the process map is reviewed to be sure that it accurately reflects the existing process.
- Apply Improvement Techniques: Challenging Everything — Companies apply the six improvement techniques, which changes the business process so that it delivers business value.
- Create Internal Controls, Metrics and Tools: Making it Real — This step is about minimizing possible errors, identifying process metrics and creating tools to automate the business process.
- Test and Rework: Making Sure It Works — Step 8 creates a plan to test the new process to ensure everything works as planned.
- Implement Change: Preparing the Organization — Communication is key here. The company must identify who needs to know about the change, what they need to know about it, and how to properly communicate the right information to the right people.
- Drive Continuous Improvement: Embracing the New Mindset — Continuous improvement is an ongoing process, not just a one-time event.
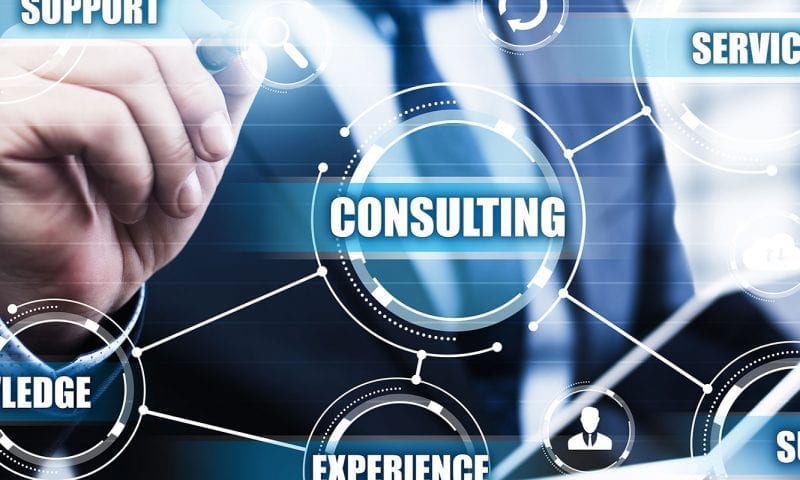
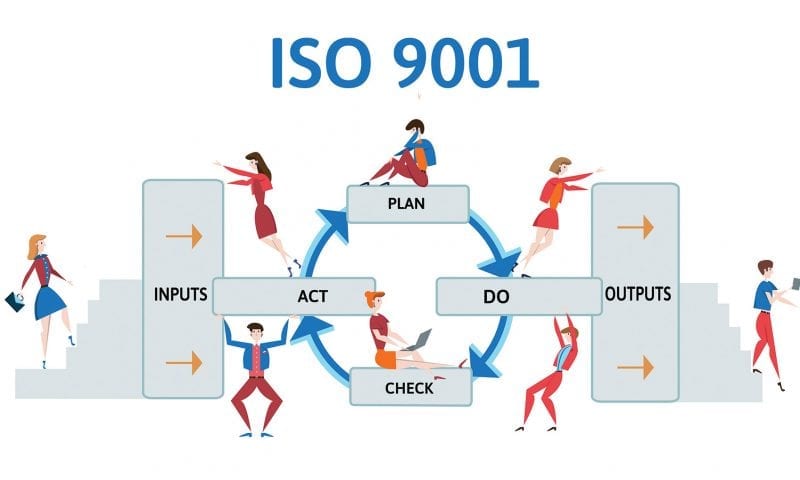
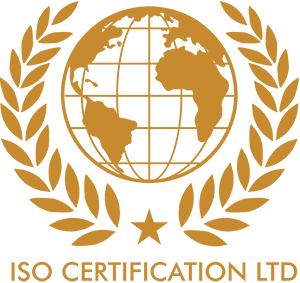
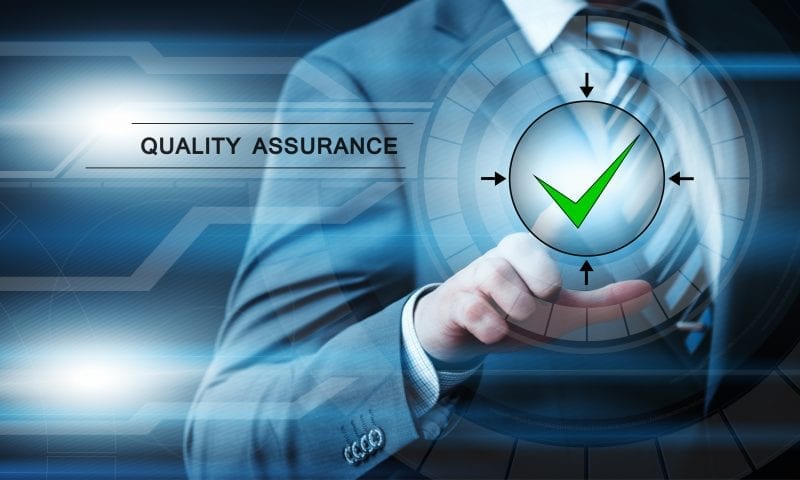
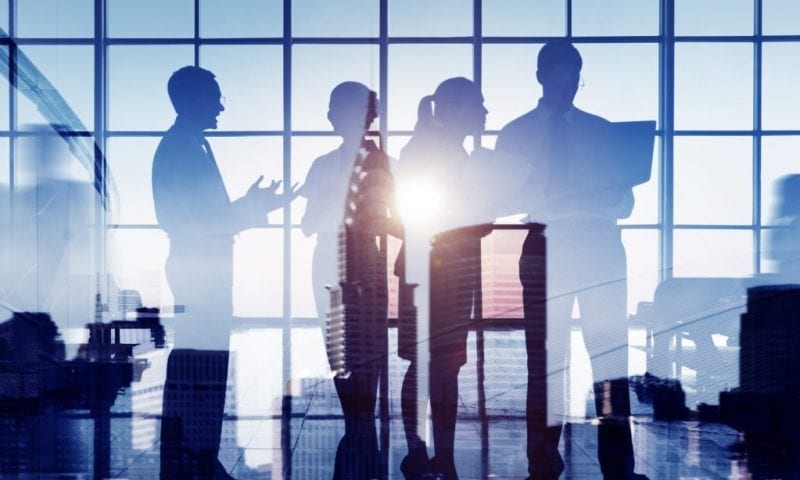
Want Expert advice on HOW TO IMPROVE YOUR BUSINESS?
We will get to know you, your business, and what you want to achieve out of your systems and your certifications.
We take care of the whole process for you, answer all your questions and adjust our services to suit your resources and your individual business needs. We will be there for you to coach you through the preparation, the audits and ongoing.
We assist in selecting your Conformity Assessment Body (CAB) to ensure they have the appropriate knowledge of your industry and the work you do, are realistic and take a value-adding approach.
We understand that every business is unique- and we want this to be a meaningful and value-adding process for you.
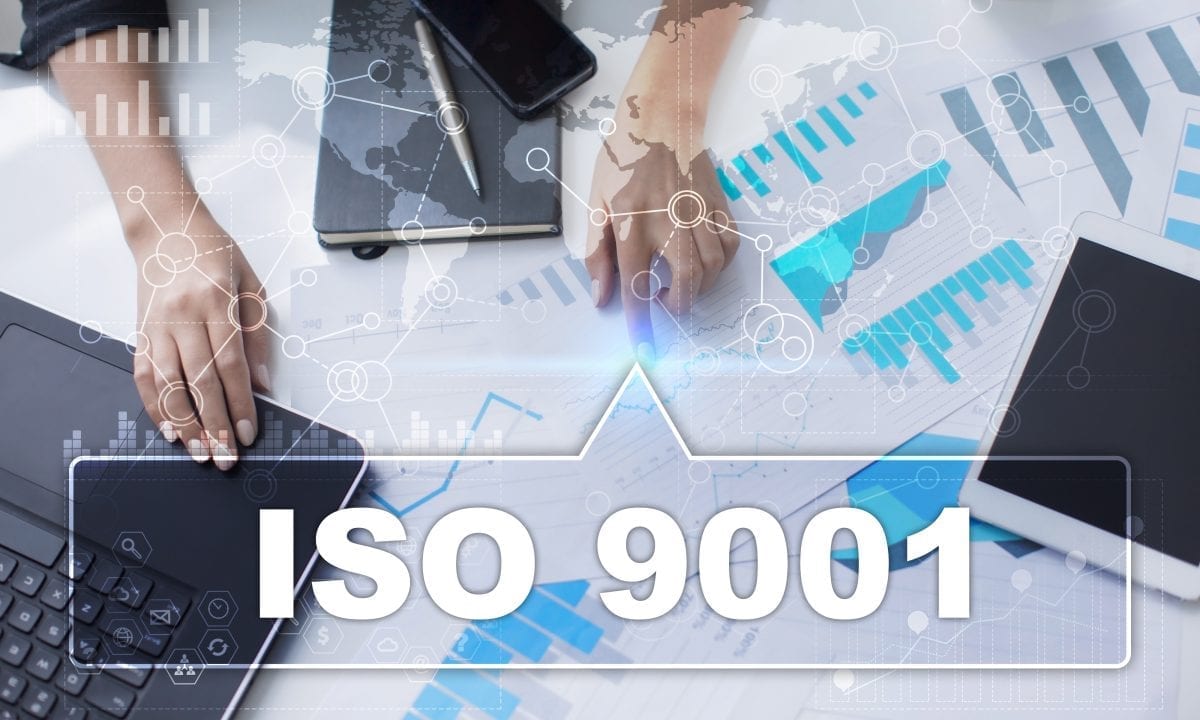
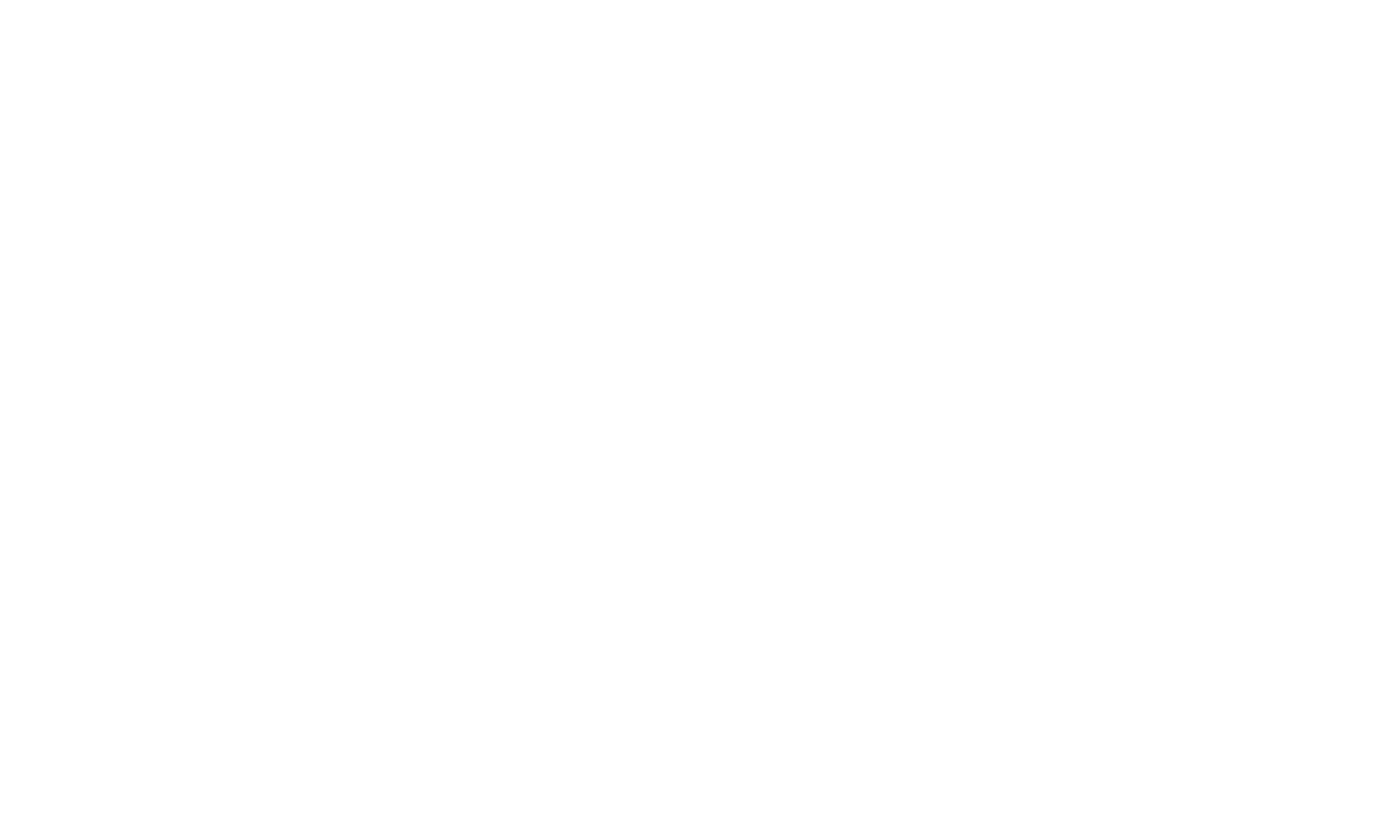